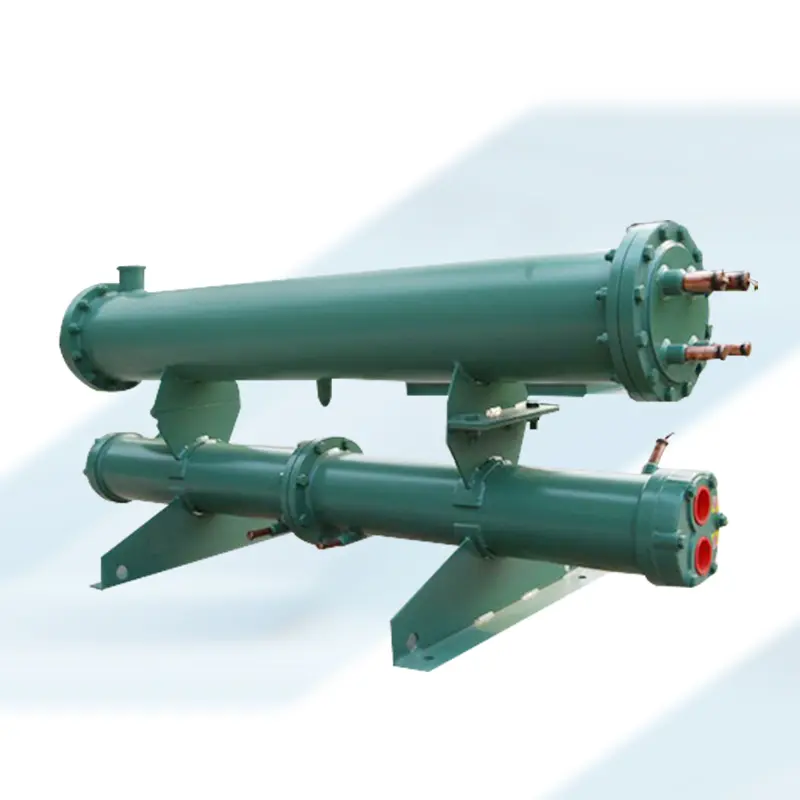
Shell and Tube Type Water Cooled Condenser for Your Thermal Exchange Needs!
Get our latest Shell and Tube Type Water Cooled Condenser – the pinnacle of efficiency and performance in the world of heat exchange technology. Designed to meet the demanding requirements of various industrial applications, our water cooled shell and tube condenser stands as a testament to innovation and precision engineering.
This condenser is used in various industrial and HVAC systems. It features a shell, which is a cylindrical outer vessel, and a bundle of tubes within it. This condenser is widely used in power plants, refrigeration systems, and chemical processes.
As one of the leading Shell and Tube Type Water Cooled Condenser Manufacturers in India, we use high-grade materials to build these products. The robust shell and precisely engineered tubes of these condensers ensure longevity even in the most demanding environments. Also, our condensers are subjected to rigorous quality control measures.
PRODUCTS GALLERY
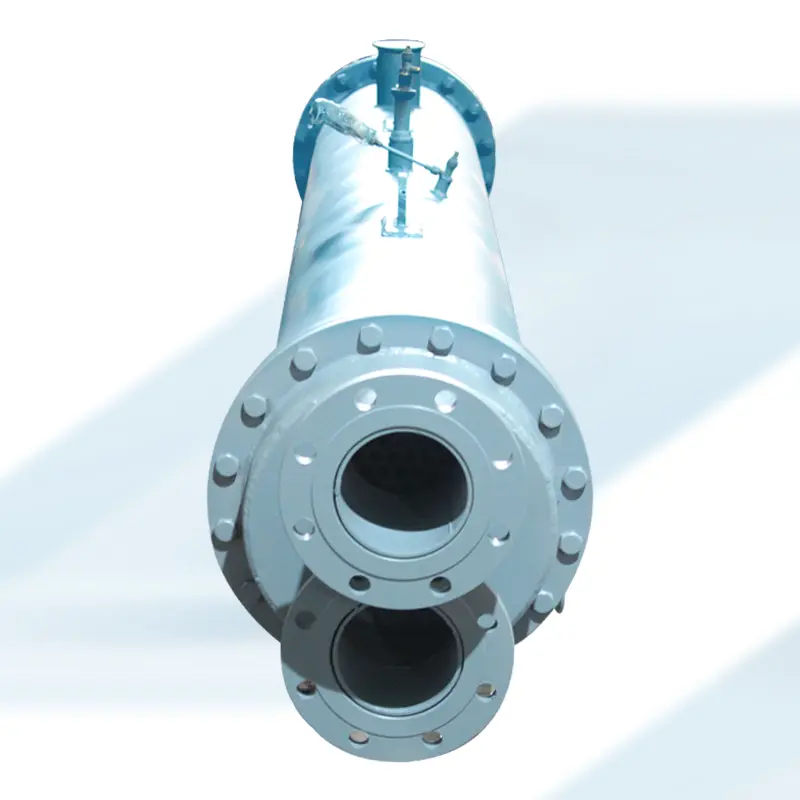
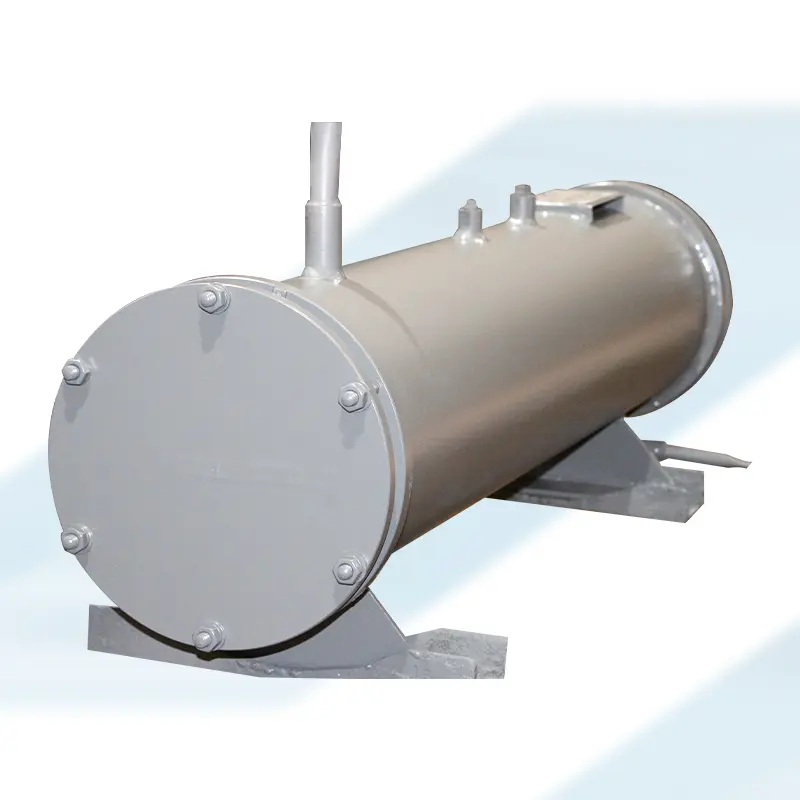
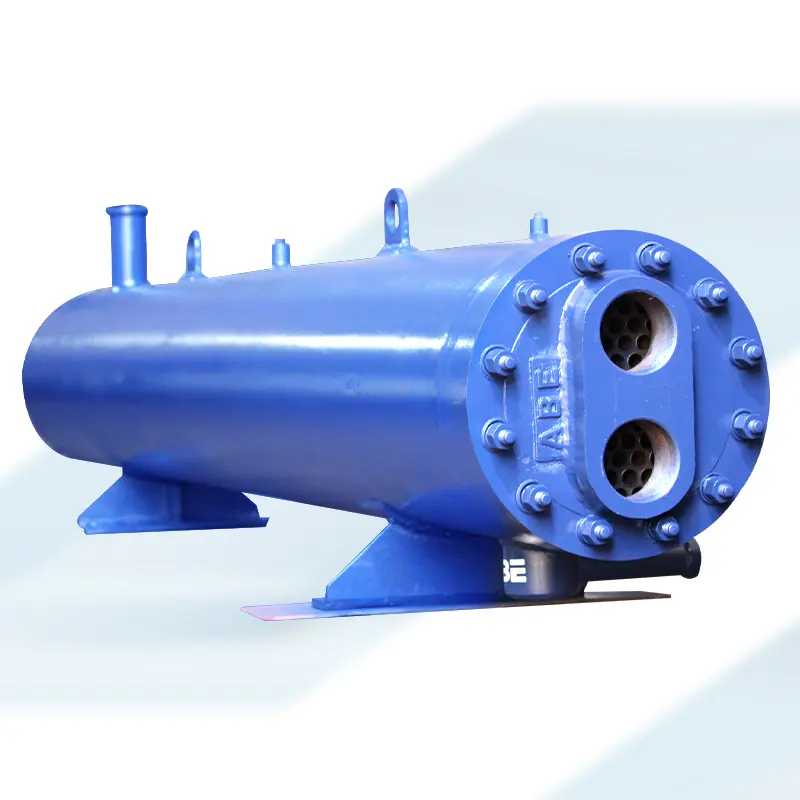

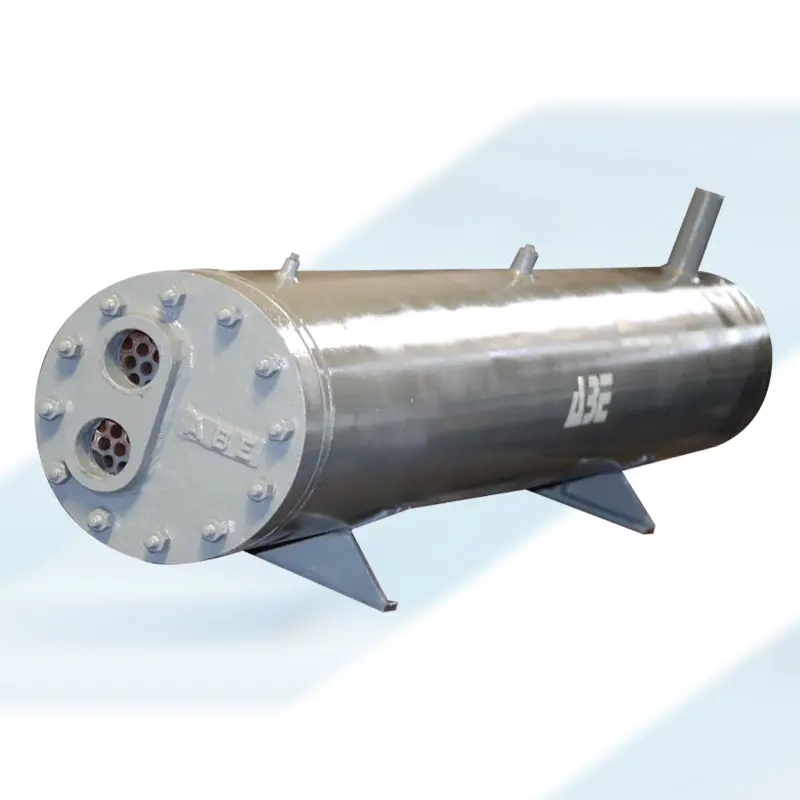
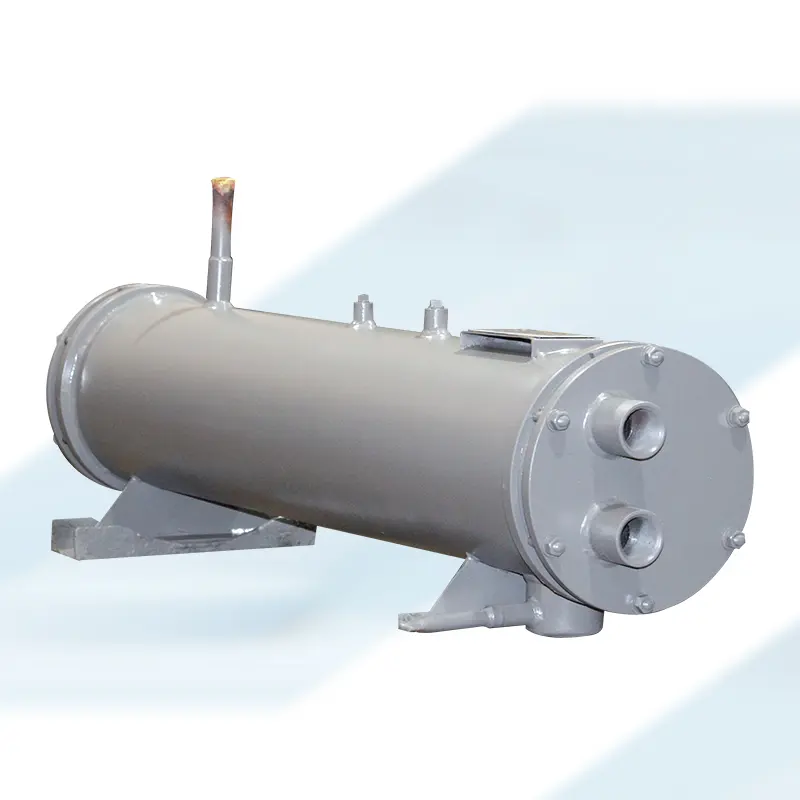
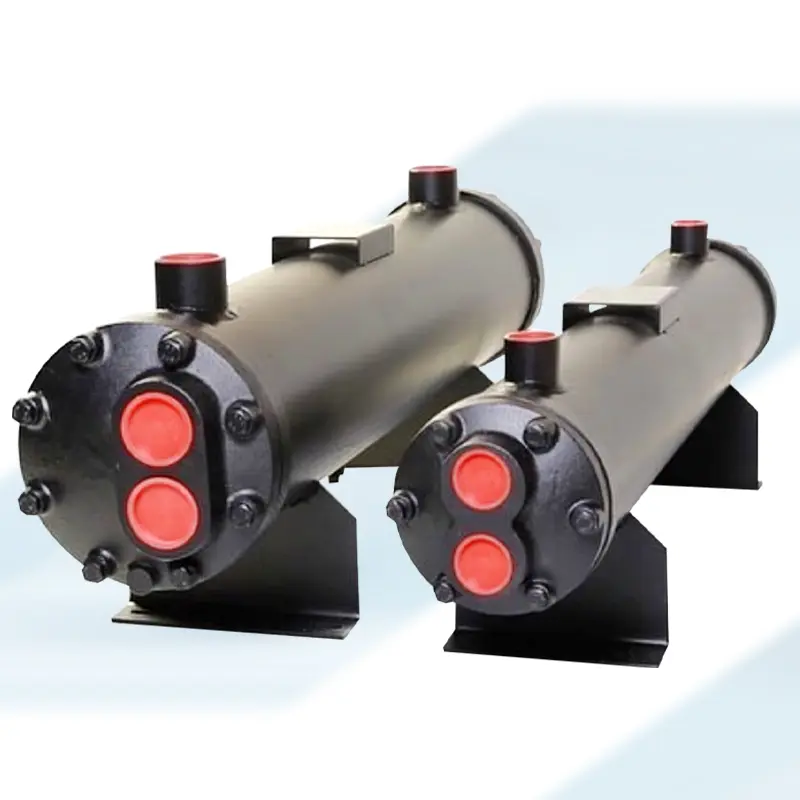

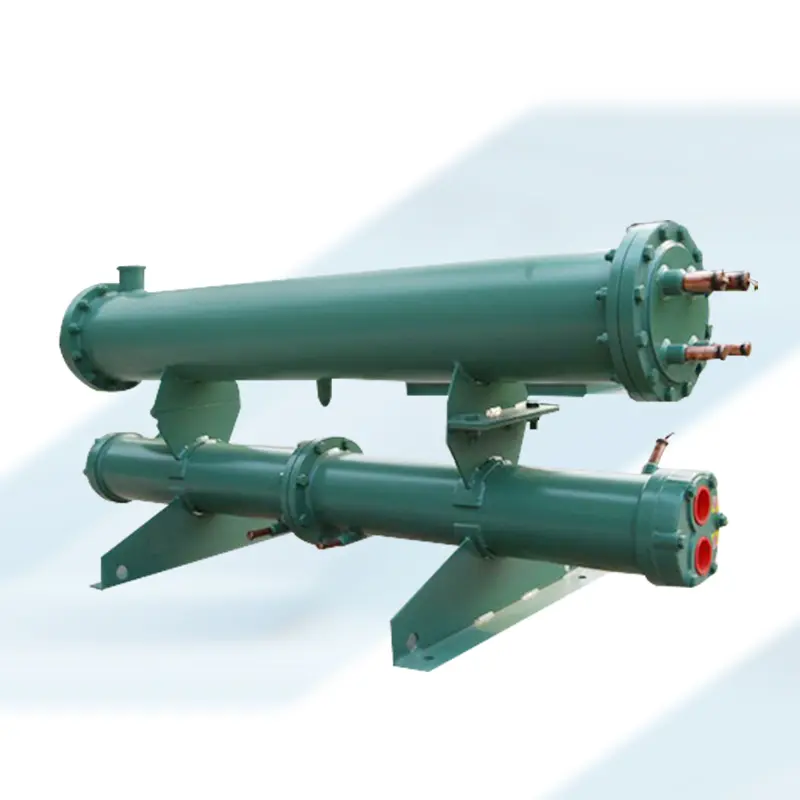
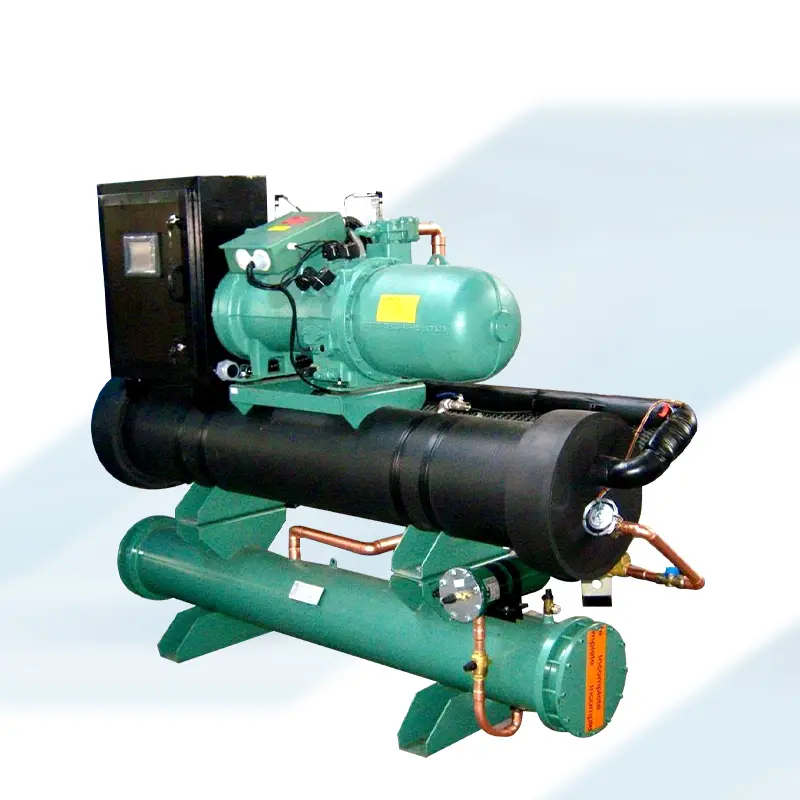
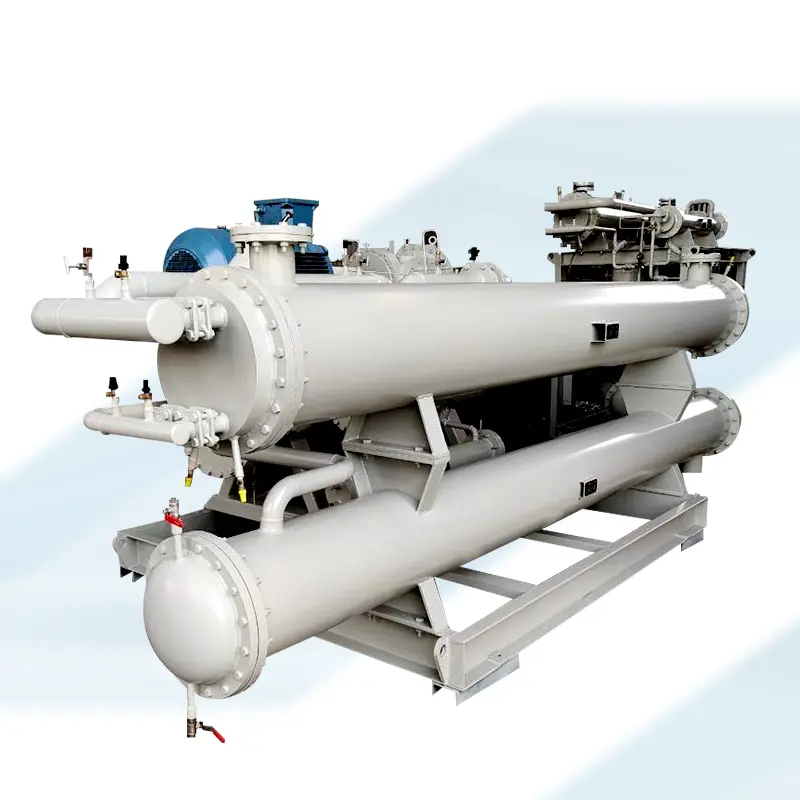
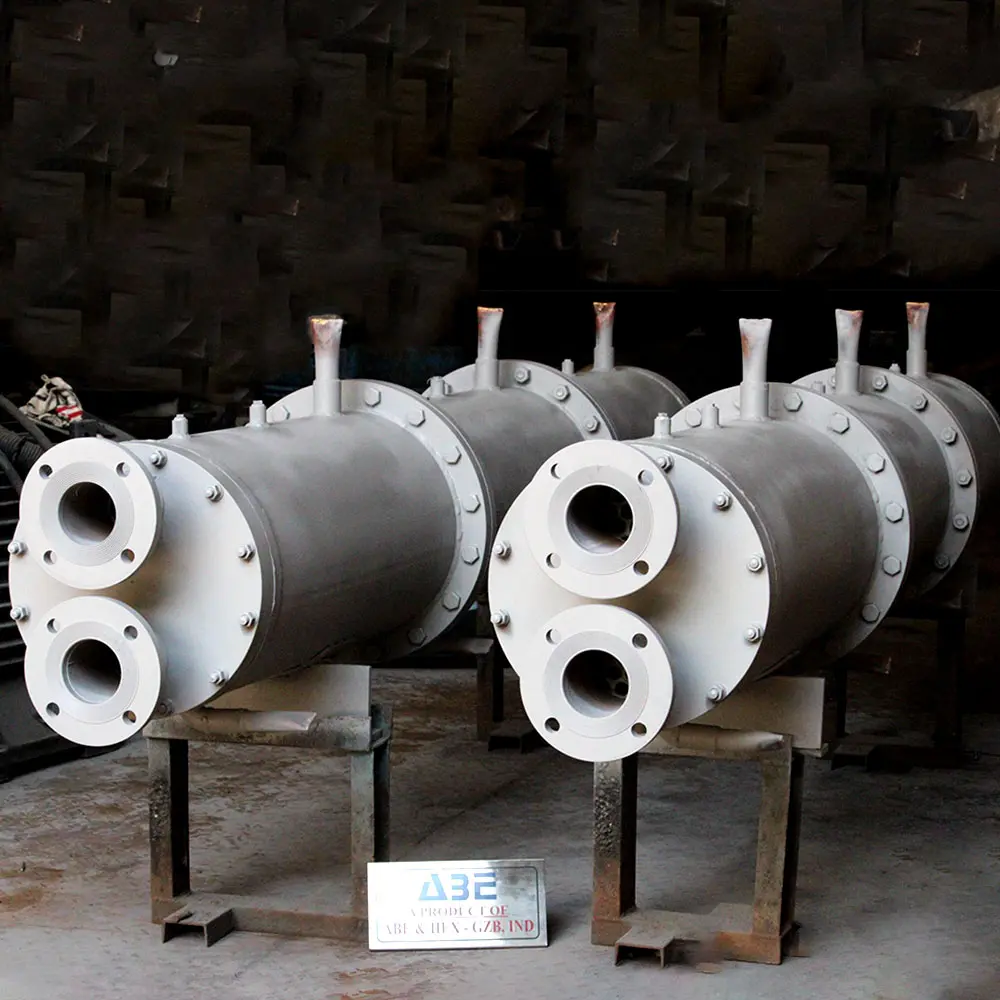
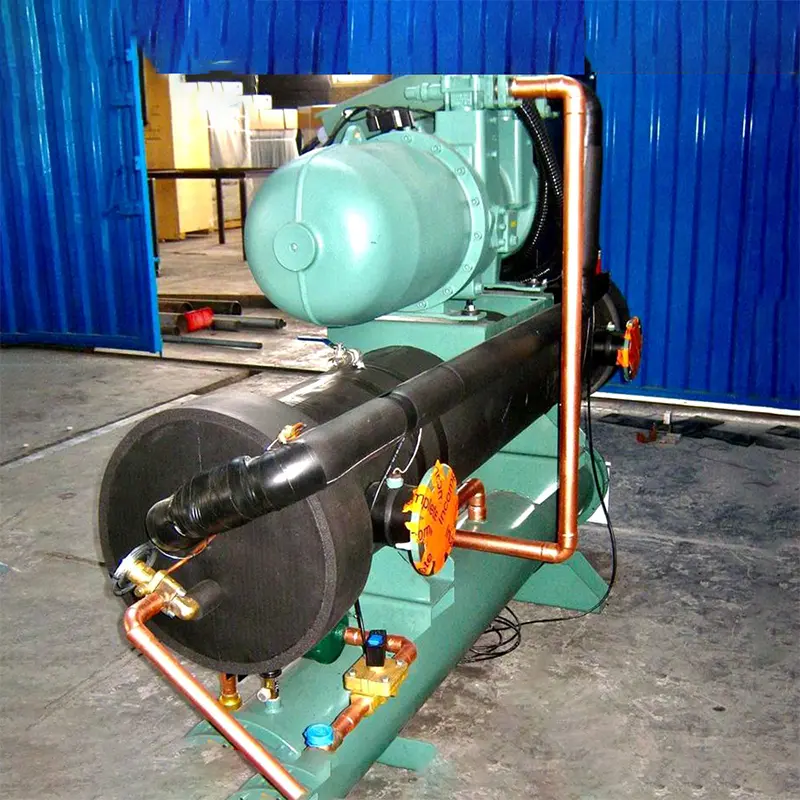
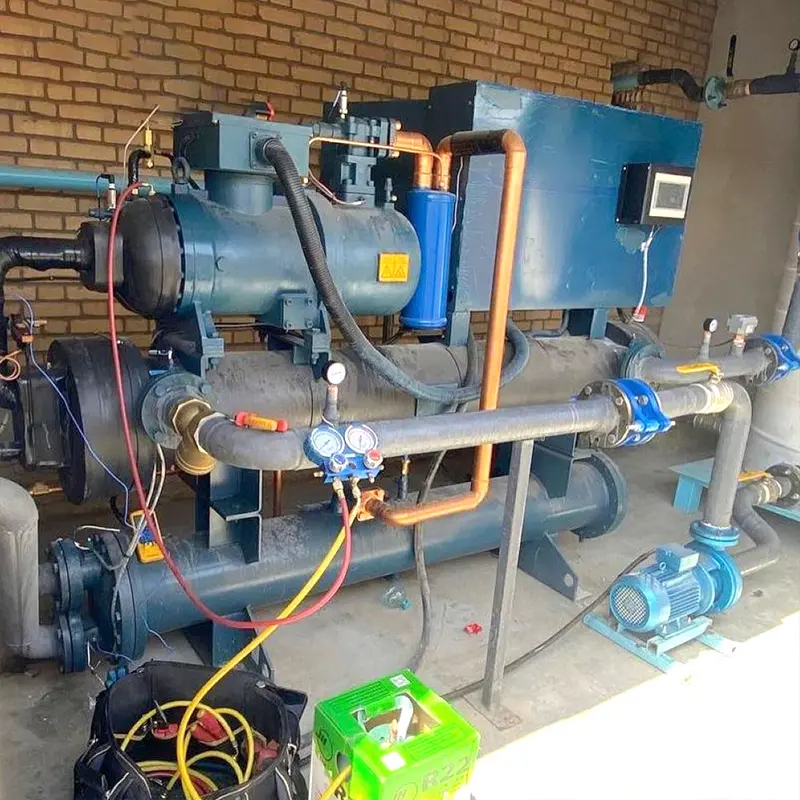

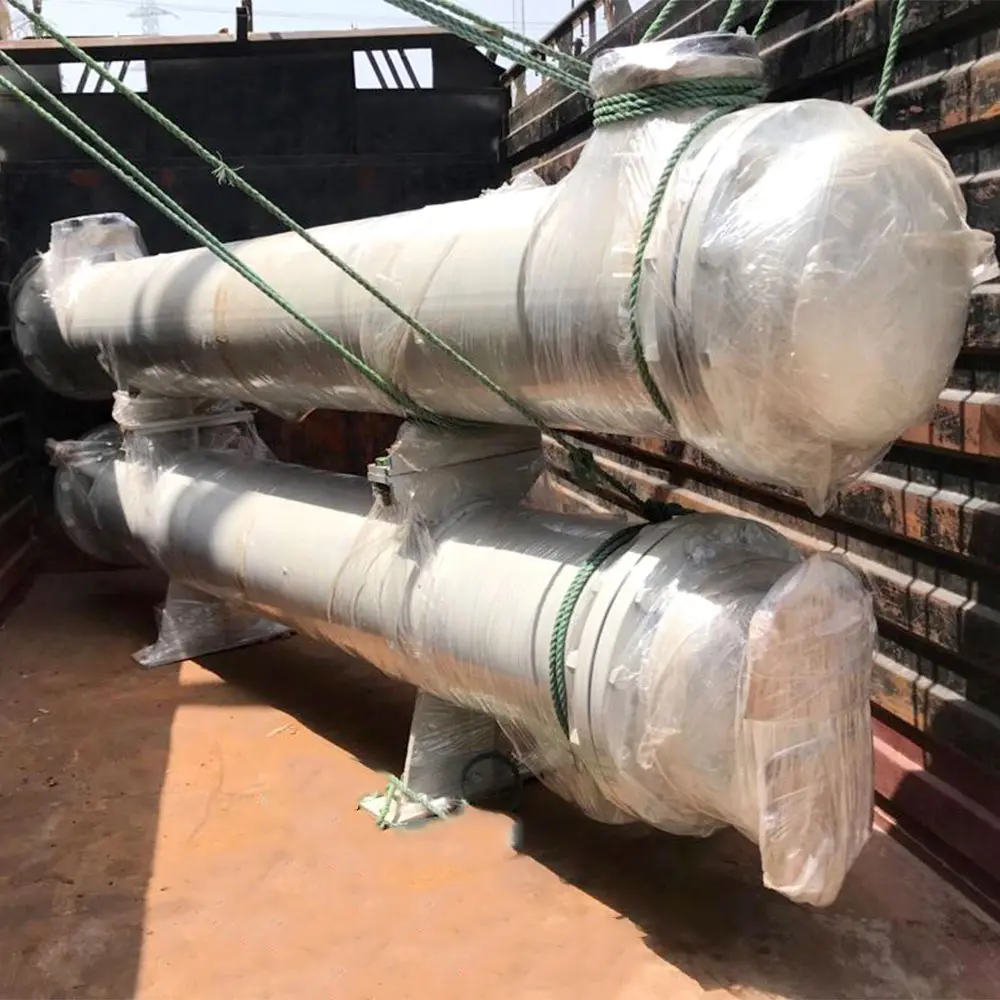
Look For the Top Brands of Shell and Tube Type Water Cooled Condensers!
We offer a range of customization options to tailor our Shell and Tube Type Water Cooled Condenser to your specific requirements. Whether it’s size, material, or special features, our team of experts is dedicated to crafting a solution that seamlessly integrates into your existing setup.
When you choose Abe & Hex India Private Limited, you’re not just investing in a condenser – you’re investing in a legacy of excellence and innovation. With a track record of delivering top-tier products to satisfied clients worldwide, we stand as one of the trusted Shell and Tube Type Water Cooled Condenser Suppliers in India. So, if you want to invest in our water-cooled condensers, contact us today to discuss your unique requirements.
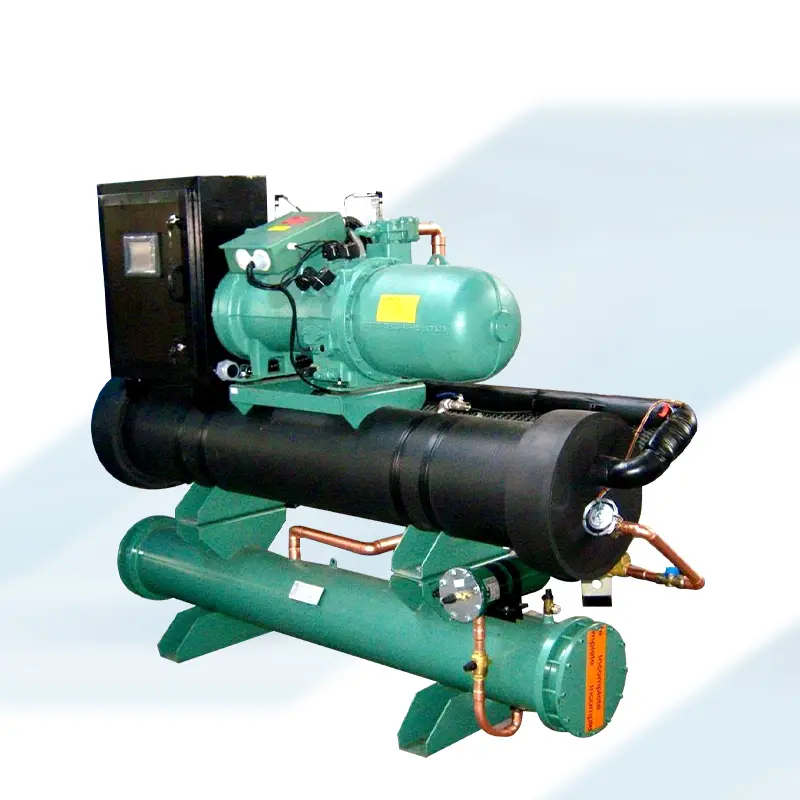
Key Features
- A Removable Shell
- Accessible Tube Bundles
- Robust and Unique Design
- High Heat Transfer Efficiency
- Versatile Application Range
- Customizable Configurations
- Easy Maintenance and Cleaning
- Crafted with Corrosion-Resistant Materials
Applications
- HVAC Systems
- Petrochemicals
- Petroleum Sector
- Natural Gas Plant
- Thermal Power Plants
- Oil & Refinery Sector
- Power Generation Plants
- Heat Processing Industry
- Chemical Processing Industry
SPECIFICATIONS
The condenser’s capacity measured in tonnes should fit the chiller system’s cooling load.
Water-cooled condensers are sensitive to the quality of the water. To avoid scaling or corrosion, it is critical to monitor and maintain the quality of the cooling water.
- Shell and Tube Condenser: A popular form of condenser in which refrigerant runs via tubes and water flows over the tubes in a shell.
- Plate Heat Exchanger: Plate heat exchangers are small and efficient condensers used in some chiller systems.
To lower running expenses, look for energy-efficient designs and features.
The condenser’s size and physical footprint should fit within the available space in the chiller plant.
The tube design for shell and tube condensers can vary, including finned tubes or smooth tubes, depending on the efficiency and heat transmission needs.
The water-cooled condenser should be constructed to support a specified cooling water flow rate, which is determined by the capacity of the chiller and the required temperature differential.
The condenser is often composed of corrosion-resistant materials such as copper, aluminum, or stainless steel.
Determine whether the condenser has integrated controls and monitoring systems for efficient operation and problem detection.
Some condenser designs may necessitate the use of fans or pumps in order to assist heat exchange or maintain adequate water flow.
Always follow the manufacturer’s installation, operating, and maintenance instructions.
The heat transfer surface area of the condenser is intended to efficiently transfer heat from the refrigerant to the cooling water.
Check that the condenser is compatible with the refrigerant type used in the chiller system.
Ensure that the condenser conforms with all applicable environmental rules and safety requirements.
It should include inlet and outlet connections for the passage of refrigerant into and out of the condenser.
Easy access to the condenser for maintenance and cleaning is critical to ensuring its long-term functioning.
The condenser will include connections for cooling water supply and return.