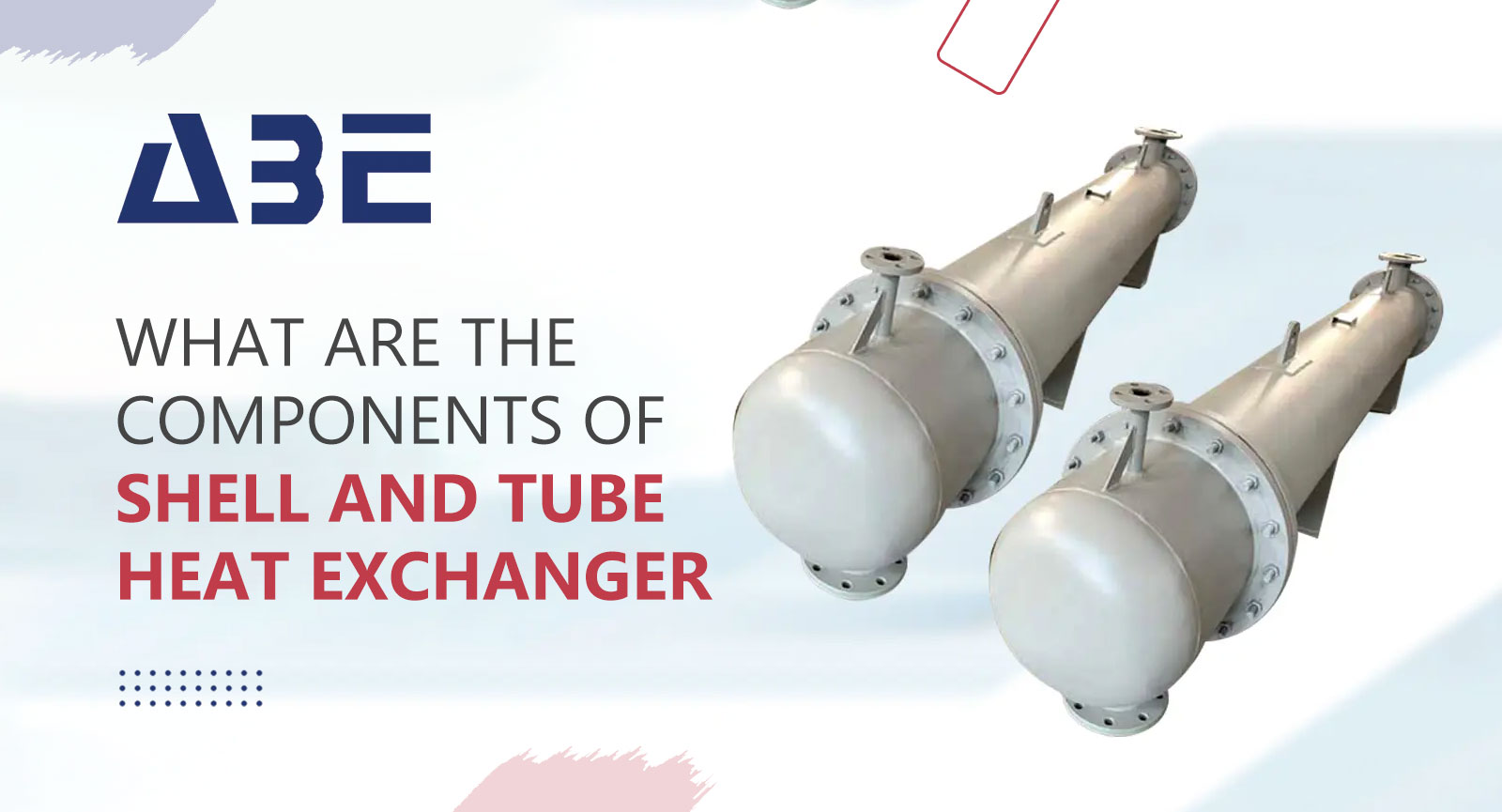
A shell and tube heat exchanger is a commonly used heat transfer system. It has a huge cylindrical shell that houses several parallel tubes. These tubes are positioned inside the shell which helps transmit heat between two fluids. Heat exchangers are popular because of their efficiency and they are available in a variety of configurations based on the application, tube design, and other characteristics.
Shell & tube exchangers are made from tubes for transferring heat between fluids at high temperatures. The tubes that give the heat exchanger its name serve as the heat transmission surface. One fluid travels through these tubes, while the other flows parallel or across them within the shell. As a result, heat is transferred across the tube surfaces.
Here are the components of a shell and tube heat exchanger:
The main components of a heat exchanger are the shell, shell cover, tubes, channel, channel cover, tube sheet, baffles, and nozzles. The Tubular Exchanger Manufacturers Association regulates the design and production requirements for shell and tube heat exchangers.
Shell
The shell is a cylinder made from either a rolled plate metal sheet or a suitable-sized pipe (up to 24 inches in diameter). Mostly, this metal is steel, although other metals and alloys may be required if the shell is exposed to high temperatures or corrosive chemicals. The shell interior is cylindrical with a consistent diameter to close the gap between the baffled perimeter and the shell itself.
Channels or Heads
The channel or head type of a shell and tube heat exchanger varies according to its use. Bonnet-type heads are commonly utilized when the head does not require frequent removal. Channels with detachable covers are flanged or welded for ease of maintenance. When the channel and tubes need to be accessed often, a detachable channel cover is necessary.
Tubes
Shell and tube heat exchangers use welded or extruded tubes composed of carbon steel, stainless steel, titanium, Inconel, or copper. Compact heat exchangers employ tubes with dimensions of 0.625 inch (16mm), 0.75 inch (19mm), and one inch (25mm). The thickness of the tubes is determined based on pressure, temperature, thermal stress, and corrosion resistance at lengths ranging from 6 to 24 feet (2 to 7 meters).
Tube Sheet
The tube sheets are forged plates with precise holes bored in them so that the tubes may be inserted and then welded into position. The shell extends beyond the tube sheets and is sealed at both ends to produce the enclosed chamber protected by the heads.
Baffles
Baffles prevent vibration, maintain tube spacing and direct fluid flow in shell and tube heat exchangers. They increase fluid velocity, which enhances heat transfer efficiency and reduces fouling. Fouling is the accumulation of undesirable materials on heat transfer surfaces that impedes heat transmission and reduces heat exchanger performance. Baffles are particularly important in horizontal heat exchangers because they support the tubes and keep them from drooping or being damaged by vibrations.
Rods & Spacers
Rods and spacers hold the baffles together and maintain the distance specified by the heat exchanger. The number of rods and spacers needed in the exchanger is determined by the number of baffles utilized and the total diameter of the shell. Tie rods are fastened to the tube sheet and span the length of the tube bundle.
ABE & HEX India Pvt Ltd is a leading shell and tube heat exchanger manufacturer in India. For further information about our heat exchangers, contact our team now.
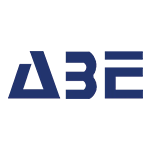
Abe & Hex India
Since 2009, ABE & HEX has been manufacturing premium quality heat exchangers. We fabricate high-grade products to meet different industrial requirements.